The Buzz on Best Fuel System Cleaner
Table of ContentsThe 30-Second Trick For Best Fuel System CleanerThe 8-Minute Rule for Best Fuel System Cleaner
If you can raise fuel pressure and still make certain that your fuel pump can provide the wanted circulation rate, then these maximum horsepower numbers will increase - best fuel system cleaner.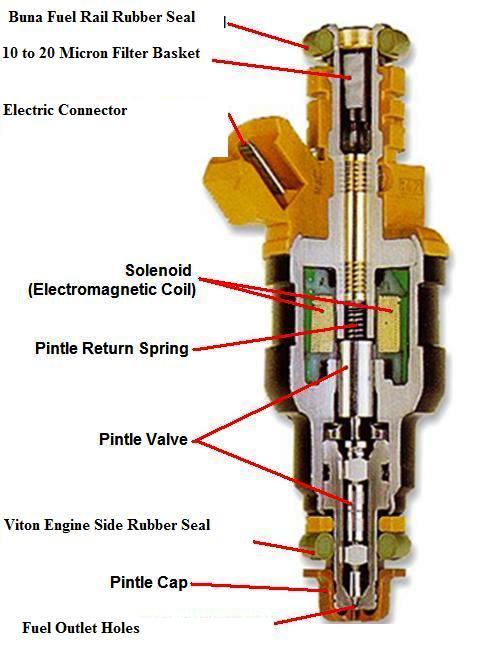

Image 2/14 This is what a washed-out common-rail injector ball seat appears like. Without a flush surface to seal against, the injector will not shut down, and piston damage is typically the result. Aggressive tuning and particles in the fuel is normally the offender. All these examples are from actual injectors Exergy Engineering took in to check.

Afton has 85 years worth of experience dealing with OEMs and fuel companies. By leveraging both of these business' proficiency, we wish to make fuel injector issues a distant memory. If correct upkeep is carried out and problematic practices are prevented, the large majority of diesel owners will go thousands of hassle-free miles without an issue.
This is since older diesel injection systems just utilize about 12 the fuel pressure modern-day engines do, and older injectors send the fuel through much bigger passages. Why is there such a distinction with common-rail injectors? Modern common-rail diesel injectors can fire 2 or three times per engine cyclethis doubles the wear on the injector compared to diesels of the past.
More About Best Fuel System Cleaner
The feedback we obtain from our readers and online reports of failures suggests there's constantly room for enhancement in our fuel, too. According to Exergy Engineering, injectors fail due to the fact that of five significant factors. We listed them here, in addition to the signs of the issue, the causes, and how it's prevented.
To the naked eye, an injector may appear great, when in truth it is not. The shim on the right was likely damaged throughout injector assembly. 1. Engine is difficult to begin (requires increased cranking time in order to begin) 2. Low common-rail pressure codes Worn injector ball seat Dripping cross feed tubes (Cummins) Blown internal high-pressure seal Incorrect nozzle needle clearance Broken nozzle body Broken injector body Keep fuel system clean, change fuel filters, purchase fuel from reliable sources, prevent filling from portable building fuel tanks Prevent extremely aggressive tuning that increases rail-pressure and injector pulse widths and do not eliminate pressure-limiting devices from the system Do not use remanufactured or aftermarket injection parts that are not properly developed or produced Decline all fuel system replacement parts that have metallic burrs Use just Bosch nozzles, as they are reported to have superior crack resistance Do not mix nozzle needles, because they are matched to the body and moving one from another can lead to excessive clearance or improper needle lift Balance rates are high (favorable), suggesting fuel is being included to the cylinder since the computer thinks the fuel injector is not flowing enough.
If the crankshaft is not spinning as quick as the computer thinks it should (or find out here is spinning quicker than it must), fuel (by means of pulse width) is included or taken away to level crankshaft velocity from each injector shooting (best fuel system cleaner). Image 4/14 Here is a blown high-pressure seal found inside a common-rail injector.
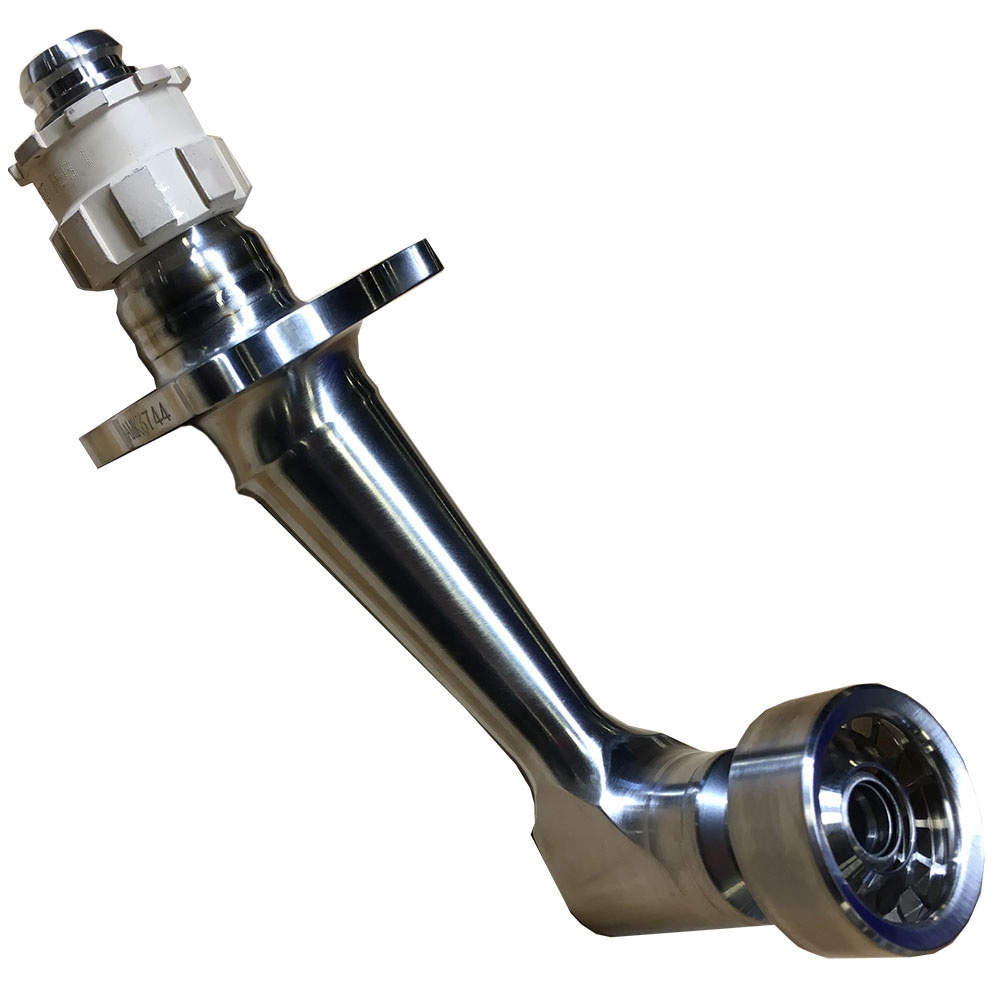
This is one of the reasons so few companies can restore common-rail injectors. Large cylinder-to-cylinder exhaust temperature variation Poor go now nozzle flow balance Nozzle needle lift inaccurate (mixed or missing parts) Partially plugged nozzle Wire-brushed nozzles Keep fuel system tidy, change filters, purchase fuel from dependable sources, and prevent filling from portable building fuel tanks or questionable sources Decline all fuel system replacement parts that have metallic burrs Do not utilize remanufactured or aftermarket elements that are not effectively developed or produced Ensure injectors are serviced or bought from a trustworthy source Do unclean nozzles with a wire brush Failure: Incorrect Injection Timing and Duration Rough running, poor cylinder balance, and knocking Piston damage Large cylinder-to-cylinder exhaust temperature variation Ball seat wear Inaccurate injector assembly, parts combined, or parts missing out on Injector needle lift increased to increase output Replace worn injectors Ensure injectors are serviced, tested, and bought from navigate to these guys a trusted source According to Afton Chemical's North American Marketing Supervisor, David Cleaver, there are 3 significant causes of injector failure connected with the homes of the fuel itself: excess wear, abrasion, and deposits.